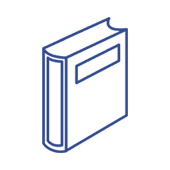
Technologia roztaczania otworów głębokich w częściach o małej sztywności
Monografia
ISBN: 978-83-7947-245-1
MNiSW
80
Poziom I
Status: | |
Autorzy: | Szot Tomasz, Świć Antoni |
Dyscypliny: | |
Rok wydania: | 2017 |
Serie: |
Monografie – Politechnika Lubelska
|
Wersja dokumentu: | Drukowana | Elektroniczna |
Język: | polski |
Liczba stron: | 147 |
Miejsce wydania: | Lublin |
Wydawnictwo: | Politechnika Lubelska |
Efekt badań statutowych | NIE |
Materiał konferencyjny: | NIE |
Publikacja OA: | TAK |
Abstrakty: | polski | angielski |